Our Infrastructure
CAD - CAM / Tool Room
We use the latest CAD software in our design center and as a result our engineers have been able to improve component benefits and interchangeability, thereby enhancing the effectiveness, quality and ergonomic.CAD - CAM
3D design software Solid Works and Espirit allow our experienced forging designers and apprenticed diesinkers to quickly go from yours files to steel, shortening the "Print to Part" lead time.Deckel Maho
70V vertical machining center with automatic tool changer having carousel magazine with 30 packets, minimizing the tool changing time. With 18000 spindle RPM which turn give high surface finish on dies and a feed of 70 meters per minute.Wire Cut
Electronica Omnicut wire cut machine with cutting speed of 80mm square per minute equipped with LM guides and hand held remote controls.CNC Vertical Machining Center
TONG TAI'S TOPPER make CNC vertical machining centre with 24 stations ATC with hydraulic clamping, FANUC conroller. Work table size 850 mm x 470 mm with XYZ travel of 760mm x 450mm x 530mm to machine any type of forging die or production component involving multi tooling in one setting.Forging Facility
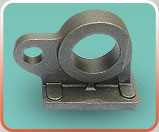
Hammers
Drop forged hammers with diffirent capacities ranging from 1000 kgs. to 2000 kgs. to forge the sophisticted Engine Components weighing from 70 gms. to 7 Kgs.Press Forging
Forging Presses of 1000 Tons (HONOUL KOREA) & 1600 Tons capacity (KURIMATO JAPAN) for Precision Forgings.Machining Facility
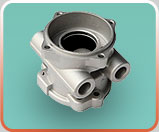
CNC Turning Centres
TONG TAI'S TOPPER make CNC turning centers to machine the components in the CP / CPK level, desired by the quality standards. The capacity of machine is maximum turning diameter 256mm, Length 400mm, & 12 station turret head with FANUC controller.Machine Shop
Modernistic machine shop comprising of various CNC turning centers and semi automatic machines to get best quality in machining of precision components.Heat Treatment Facility
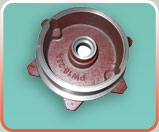
At Sanmati Forge Cast castings can be heat-treated to bring about diffusion of carbon alloying elements, softening, hardenings, stress-relieving, toughening, improved machinability, increased wear resistance, and removal of hydrogen entrapped at the surface of the casting.
Steel's versatility is due to its response to thermal treatment. Heat treatment greatly increases the number of properties that can be obtained, because at certain 'critical temperatures' iron changes from one type of crystal structure to another. This structural change, known as allotropic transformation, is spontaneous and reversible and can be made to occur by simply changing the temperature of the metal.
Fundamentally, all steel heat treatments are intended to either harden or soften the metal. They involve one, or a series of operations, in which solid metal is heated and cooled under specific conditions to develop a required structure and properties. In general, the following major forms of heat treatment, for the standard steels, are used to modify properties to suit either fabrication or end use; Quenching, Tempering, Normalizing, Annealing and Stress Relieving.
To provide steel castings with the properties mention above, Sanmati Forge Cast Company has installed a modern heat-treating facility which allows the following types of heat treatments to be performed:
- Water Quenching
- Tempering
- Normalizing
- Annealing
- Stress Relieving
In addition, the following services can be provided upon request:
- Oil Quenching
- Atmospheric Carburizing
- Flame Hardening
The heat-treating facilities at Sanmati Forge Cast consist of the following major components; three (3) 7' x 12' Car Bottom Furnaces equipped with automatic recording pyrometers, a high temperature gas fired Box Furnace (stainless), a 6,800 gallon capacity quench tank which includes a 2,200 gpm water circulation pump and 16,000 gallon capacity water reservoir and a dedicated Brinell testing line.
Non Destructive Testings
Non Destructive Testing is a descriptive term used for the examination of materials and components in such a way that allows materials to be examined without changing or destroying their usefulness.
Visual Inspection
Visual inspection is the one NDT method used extensively to evaluate the condition or the quality of a weld or component. It is easily carried out, inexpensive and usually doesn't require special equipment.
Magnetic Particle Inspection
Magnetic particle inspection is a method that can be used to find surface and near surface flaws in ferromagnetic materials such as steel and iron.
The technique uses the principle that magnetic lines of force (flux) will be distorted by the presence of a flaw in a manner that will reveal it's presence. the flaw (for example, a crack) is located from the "flux leakage", following the application of fine iron particles, to the area under examination. There are variations in the way the magnetic field is applied. but they are all dependant on the above principle.
Ultrasonic Inspection
Ultrasonic inspection uses sound waves of short wavelength and high frequency to detect flaws or measure material thickness.
Radiographic Inspection
X-ray or gamma rays are placed close to the material to be inspected and they pass through the material and are then captured on film This film is then processed and the image is obtained as a series of gray shades between black and white. Careful inspection of the film will revel internal flaws that may not be found by other inspection methods.
Designing & Pattern Making › We have MAGMASOFT Software giving foolproof methods for designing and patterns, a well equipped Pattern Shop and Ancillaries for making Wooden, Metallic and Shell Patterns.
Melting Shop › A Battery of Medium Frequency Induction Furnaces of 3 tons & 2 tons capacity for Sand Castings and 2 nos. each of 500 kg capacity Induction Furnaces for Shell Molded Castings.
Molding Shop › We have complete sand conditioning plants with 7.5 tons and 10 tons per hour capacities and facilities for Machine Molding including a 4.5 ton Floor Jolter, High productivity ARPA 1300 Molding machines for box sizes 500 mm to 1200 mm for Green Sand, Sodium Silicate / CO2 sand and Nobake sand. We also have 18” x 27” and 24” x 30” Shell Molding machines for Shell Molded Castings. Additionally we also have a fully equipped Core shop with Electric Core Oven having Digital Temperature control system. Our cores are manufactured in Oil Sand, CO2 and Nobake by Shell Process.
Fettling Shop › Pencil Hand Grinders to Heavy Swing Frame Grinders with facilities for welding AC and DC with pre-heating arrangement; Air Arc Gouging and Shot Blasting facilities. Hydraulic Press for straightening of castings.
Heat Treatment › For Heat Treatment we have a battery of Oil fired furnaces having capacities of up to 7 tons per charge and a maximum operating temperature of 1100°C with an arrangement of automatic multipoint temperature recording of various zones of each furnace. We also have facilities for Water Quenching and Polymer Quenching.
Hydraulic Press Shop › BEMCO make Hydraulic presses capacity 250 tons with in built Die Cushioning.
Press Shops › Systematic press shop equipped with pneumatic and mechanical controlled presses having capacity range 05 tons to 250 tons.
Machine Shop › We have a full fledged state-of-the-art in-house Machine Shop with the following machinery: Machine Shop
In a quest to move its products up the value chain and satisfy customers demand for finished components, M is upgrading its machine shop into a state-of-the-art machining facilities which includes :
- CNC Turning Centers
- CNC Vertical Machining Centers (VMCs)
- Special Purpose Machines (SPMs)
- Radial Drilling Machines
- Lathes
- Milling Machines

